平齒機自動對刀技術:減少人工干預的3種實現路徑
在齒輪加工領域,平齒機的對刀精度直接影響齒輪嚙合性能與加工效率。傳統人工對刀依賴操作者經驗,存在效率低、一致性差等問題。隨著智能制造發展,通過自動對刀技術減少人工干預成為行業趨勢。以下是三種典型實現路徑:
1. 基于傳感器的實時監測技術
通過高精度位移傳感器(如激光傳感器、電容式傳感器)實時采集刀具與工件的相對位置數據,結合閉環控制系統實現自動補償。例如,在刀具接觸工件瞬間,壓力傳感器可檢測微小接觸力變化,觸發數控系統記錄初始位置并完成對刀。該方法響應速度快(可達微秒級),但需解決傳感器抗干擾問題,適用于加工環境穩定的場景。
2. 機器視覺輔助定位系統
采用工業相機采集刀具刃口圖像,通過邊緣檢測算法提取特征點坐標,結合標定參數計算刀具空間位置。德國某廠商開發的VisionTool系統,通過亞像素級圖像處理技術,可實現±2μm的定位精度。此技術尤其適用于復雜輪廓刀具,但需配合高分辨率光學鏡頭和防抖裝置,成本較高。
3. 自適應智能算法驅動
利用機器學習算法建立加工參數與刀具磨損的映射關系,通過振動、聲發射等信號實時預測刀具狀態。日本FANUC的AI伺服系統,可基于歷史數據自動優化對刀路徑,減少30%的空行程。該技術需構建完善的數據采集體系,結合數字孿生技術可實現預測性維護,代表未來智能化發展方向。
當前,行業正從單一技術應用向多模態融合演進。例如,將視覺定位與力覺反饋結合,可提升復雜工況下的適應性;嵌入5G模塊后,還能實現遠程對刀參數優化。隨著工業4.0深入,自動對刀技術將成為齒輪加工單元向智能工廠升級的突破口,推動行業從"經驗驅動"向"數據驅動"轉型。企業需根據加工精度要求、成本預算等因素,選擇適宜的技術路徑分步實施。
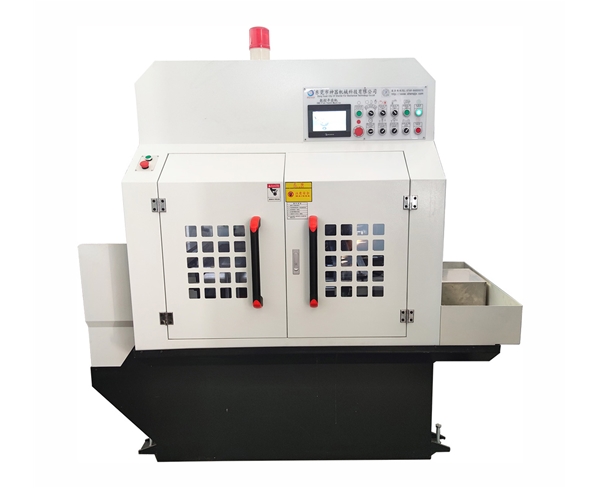